Eppendorf Dasgip Bioblock System
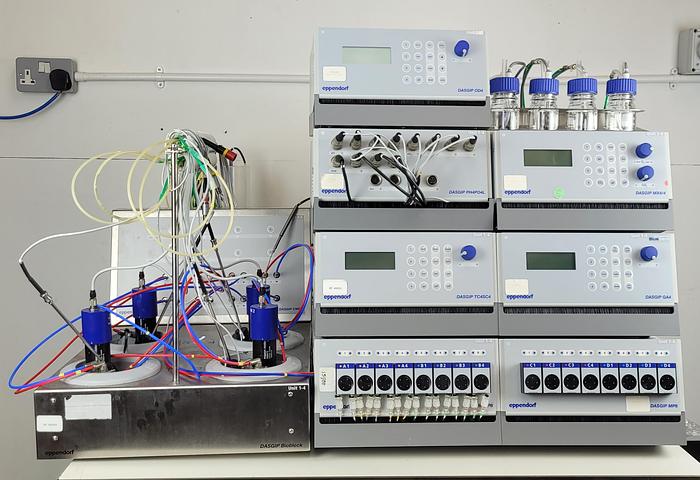
Eppendorf Dasgip Bioblock System
Contact us for price
Location:Duxford, United Kingdom
Available quantity:1
Description
This listing is for a Eppendorf Dasgip Parallel bioreactor system
NB. Variations in specification occur subject to applications required. Please check the images and contact us if unsure
The unit is in full working condition and is ready for immediate release
2 x DASGip OD4 Optical density Monitor
1x PH4P04L V2.1 Sensor Module
1 x MX4/4H V2.1 Gas Mixing System (250 sL/h Max)
1 x TC4SC4 V2.1 Temperature and Agitation Controller
2 x DASGIP MP8 Multi Pump Module
PC, monitor, Power Supply. USB Unchecked
Key Features
Parallel Bioreactor Setup:
Operates multiple bioreactors (2, 4, 6, or 8) simultaneously, providing high-throughput experimentation for cell culture and microbiology applications.
Ideal for testing various conditions (temperature, pH, gas supply, nutrient concentration, etc.) in parallel, accelerating process development and optimization.
Advanced Bioprocess Control & Automation:
Precise Control of critical parameters like pH, temperature, dissolved oxygen (DO), agitation, and foam for optimal bioprocessing conditions.
User-Defined Profiles: Customize and define specific process profiles (e.g., growth phase, fed-batch protocols) for automation, ensuring consistent results across all bioreactors.
Automated Control of feeding rates, gas mixing, and environmental conditions, reducing manual intervention and increasing reproducibility in experiments.
Real-Time Data Monitoring: Continuous tracking and analysis of parameters to provide insights for advanced process optimization.
Parallel Processing for Accelerated R&D:
Simultaneous Trials: Conduct multiple experiments at once, allowing for the optimization of different process variables, such as media composition, agitation speeds, and pH.
This parallel processing capability accelerates research cycles and enables more efficient R&D workflows.
Highly Efficient Process Development:
Cell Culture and Microbiology: Supports a wide range of applications from mammalian cell culture, bacterial, yeast fermentation, and insect cell cultures, making it suitable for both biotech and pharmaceutical industries.
Optimize the growth conditions for various cell lines, yeast strains, or bacteria with fine-tuned control over parameters.
Transition from lab-scale research to process scale-up with ease, reducing the time and costs associated with scale-up trials.
Precision Control of All Relevant Parameters:
Temperature Control: Independent control of each bioreactor’s temperature for precise environmental control.
pH and pO2 Monitoring: Real-time measurement and automated adjustments of pH and dissolved oxygen for cell culture or fermentation optimization.
Agitation: Adjustable agitation speeds to optimize mixing, oxygen transfer, and cell growth conditions for both cell culture and microbiology.
Foam Control: Integrated foam sensors and anti-foam pumps to maintain optimal conditions without disruptions to the process.
Automation Features:
Automated Media and Feed Control: Automated media addition and feed control systems, ensuring the precise delivery of nutrients and growth factors, enhancing growth performance and minimizing variability.
Synchronized Feeding and Sampling: Synchronize nutrient or feed injections with the growth phases of the culture, and automate sampling processes for accurate data collection and analysis.
Modular and Scalable System:
Flexible Configuration: Choose from configurations with 2, 4, 6, or 8 bioreactors, allowing you to tailor the system to your specific needs.
Scalability: The system is scalable for lab-scale applications and process development, with options to transition seamlessly from small-scale to pilot-scale operations.
Gas Mixing & Flow Control:
Gas Supply: Adjustable gas flows for oxygen, nitrogen, and carbon dioxide, enabling fine control over the atmospheric conditions within each bioreactor.
Gas Mixing Stations: Designed to ensure optimal gas compositions, critical for cell growth and fermentation processes.
Data Logging and Analysis:
Advanced Data Logging: All parameters are logged and stored for future reference, with the ability to track and analyze trends over time.
Comprehensive Process Tracking: Full traceability of experiments and process conditions to ensure reliable data for process development and optimization.
User-Friendly Software Interface:
DASGIP Control Software: Intuitive software interface for managing bioreactor setups, process control, and data logging. Provides tools for recipe management, real-time parameter adjustments, and data analysis.
Remote Access: The system can be controlled remotely, enabling easy access and management of experiments from any location.
Components of the DASGIP Parallel Bioreactor System
Bioreactor Vessels:
Control Stations:
Independent control stations for each bioreactor, allowing precise and individual control of critical parameters (temperature, pH, DO, agitation).
Gas Mixing and Flow Control:
Gas Mixing Stations: Provide flexible control over oxygen, CO₂, nitrogen, and other gas supplies.
Flow Controllers: For adjusting the gas flow rates according to process needs.
Sensors:
pH Sensors: For continuous, real-time pH monitoring and adjustments.
Dissolved Oxygen (pO2) Sensors: Ensures oxygen levels are maintained for optimal growth.
Temperature Sensors: Provide accurate and real-time feedback on vessel temperatures.
Foam Sensors: Detect foam build-up to prevent overflow and maintain sterile conditions.
Automated Pumps and Sampling Systems:
Peristaltic Pumps: For controlled media and feed delivery.
Automated Sampling Systems: To collect samples at predefined intervals without disrupting the bioreactor environment.
Software Integration:
DASGIP Control Software: Centralized software for control and data logging, allowing users to define profiles, adjust parameters, and track processes efficiently.
Recipe Management: Customize and store specific bioprocess recipes for future use and consistent results.
Applications of the DASGIP Parallel Bioreactor System
Biotech & Pharmaceutical R&D:
Cell Culture: Ideal for optimizing cell growth, protein production, and monoclonal antibody development in mammalian cells.
Vaccine Development: Efficient testing and optimization of growth conditions for viral vectors used in vaccine production.
Biologics: Scalable processes for protein expression, antibody generation, and gene therapy research.
Microbial Fermentation:
Bacteria & Yeast Cultures: Perfect for optimizing fermentation conditions for the production of biofuels, enzymes, and antibiotics.
Fermentation Optimization: Test and adjust process parameters to enhance yield and productivity in microbial fermentation.
Process Development & Scale-Up:
High-Throughput Screening: Enables rapid screening of different process conditions for both cell cultures and fermentation, speeding up the process development cycle.
Scalability: Transition research from lab-scale to pilot-scale bioreactor systems for commercial production.
Agrochemical & Food Production:
Fermentation of Nutraceuticals: Optimize conditions for the production of vitamins, probiotics, and other bio-based products.
Food Biotechnology: Streamline the production of fermented foods such as yogurt, kefir, and other fermented products.
Specifications
Manufacturer | Eppendorf |
Model | Dasgip Bioblock System |
Condition | Used |
Serial Number | DAS3006951+ |
Stock Number | 48649+ |